
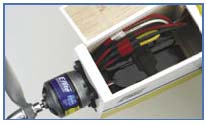 |
We added a hatch on top of the Ultra Stick 40’s fuselage (just ahead of the wing), with a tape hinge on one side, to provide quick and easy access to the battery packs. The two THP42002S2PPL pack are placed in the nose side-by-side, mounted to the fuselage fl oor (doubled with 1/8” Lite Ply) with Velcro and additionally secured using a Velcro strap that passes through the fl oor and around the battery packs. A “Y” harness built with 3” sections of 12GA wire and Deans Ultra Plugs (WSD1300) is used to join the two 2S2P packs in series as a single 4S2P pack to provide the required input voltage to the Power 46 motor. |
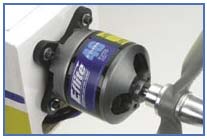 |
We installed the Power 46 using its included X-mount and hardware after drilling holes for the mounting screws/blind nuts and adding an opening in the bottom of the fi rewall to allow cooling air to pass over the batteries and ESC. A cooling air exit (about twice the size of the cooling air entrance) was opened in the bottom of the fuselage just behind the servos for proper fl ow-through and aerodynamic performance. |
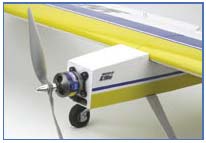 |
With the APC 13x8E prop installed using the motor’s included prop adapter, our electric power system equipped Ultra Stick 40 ARF is ready to fl y. With power and duration comparable to that of the glow .46 powered version, the only things missing are the noise and exhaust as the Power 46 motor delivers smooth, quiet and clean power, flight after flight! | | There is certainly no doubt that electric-power-system alternatives for what are typically glow engine powered models are becoming more popular and available each day. But even with the increase in popularity and availability of high-performance electric-power systems that many times provide performance equal to (and, in some cases, even better than) common glow engine setups, there are a lot of questions left to be answered when it comes to choosing and installing the right motor, prop, ESC and battery pack. The first step in fi nding the right electric-power system for your model is to determine the model’s power requirements. ‘Power’ can be measured in ‘watts’, as seen in this example:
1 horsepower = 746 watts
Watts can be determined by multiplying ‘volts’ times ‘amps’:
10 volts x 10 amps = 100 watts
We can determine the power requirements for a given model based on these Input Watts Per Pound Guidelines (using the RTF weight of the model, including battery pack):
• 50–70 watts per pound: Minimum level of power for decent performance, good for lightly loaded slow fl yer and park fl yer models
• 70–90 watts per pound: Trainer and slow fl ying scale models • 90–110 watts per pound: Sport aerobatic and fast fl ying scale models
• 110–130 watts per pound: Advanced aerobatic and high speed models
• 130–150 watts per pound; Lightly loaded 3D models and ducted fans
• 150–200+ watts per pound: Unlimited performance aerobatic and 3D models
As a note, these input watts per pound guidelines have been developed based on the typical performance of E-fl ite™ brushless motors. These guidelines may vary depending on the use of other motors as a direct result of actual motor effi ciency and prop size/effi ciency. With these guidelines in mind, we can determine the Input Watts Per Pound required to achieve the desired level of performance for a given model. Let’s take a look at how this works using a popular example.
With this info in hand, we can now find a suitable motor based on the model’s power requirements. The following tips can help you determine the power capabilities of a particular motor and if it can provide the power your model requires for the desired level of performance:
• Most manufacturers will rate their motors for a range of cell counts, continuous current and maximum burst current.
• In most cases, the input power a motor is capable of handling can be determined by using the range of cell counts, continuous current and maximum burst current ratings per the manufacturer for reference:
Average Voltage (depending on cell count) x Continuous Current = Continuous Input Watts
Average Voltage (depending on cell count) x Max Burst Current = Burst Input Watts
And here are few quick tips to keep in mind when determining the average voltage of a given pack to use in your calculations:
• The typical average voltage under load of a Ni-Cd/Ni-MH cell is 1.0 volt. The typical average voltage under load of a Li-Po cell is 3.3 volts. This means the typical average voltage under load of a 10-cell Ni-MH pack is approximately 10 volts and a 3-cell Li Po pack is approximately 9.9 volts. Due to variations in the performance of a given battery, the average voltage under load may indeed be higher or lower. These, however, are good starting points for initial calculations.
Now we revisit the model example for which we have determined the required Input Watts Per Pound, along with the ratings of a motor that could potentially be used to power the model, in order to determine if the motor can provide the desired level of performance.
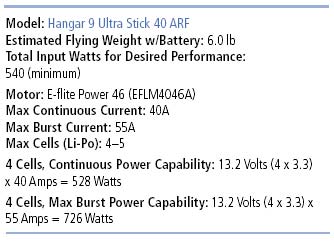
Per this example, the Power 46 motor (when using a 4S Li-Po pack) can deliver up to 726 watts of input power, readily capable of powering the Ultra Stick ™ 40 with the desired level of performance (requiring 540 watts minimum).
Of course, you must also be sure that the battery chosen for power can adequately supply the current requirements of the power system in order to achieve the desired performance. We suggest the use of Thunder Power Pro Lite Li-Po packs, as they offer the highest power-to-weight ratio of any Li-Po packs in their class and clear ratings of true maximum continuous and burst current capabilities. In some cases, Ni-MH 1950–3800mAh high- discharge packs also make good alternatives at the expense of added weight and lower capacity, but also at a lower price than their Li-Po counterparts.
Having now determined that the E-flite ™ Power 46 motor (when using a capable 4S Li-Po pack for power) can provide the desired level of performance for our chosen model, let’s take a look at how this system performs when using the recommended APC 13x8E (electric series) prop. All current, voltage and wattage measurements were taken at full throttle using an E-fl ite ™ Power Meter (EFLA110).
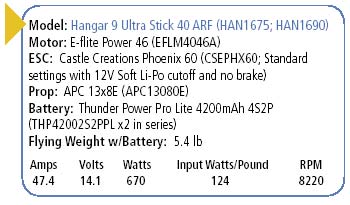
Performance of the Ultra Stick ™ 40 using this setup is even better than the minimum level of performance we set out to achieve. Very short takeoff rolls with a great balance of thrust (a nearly 1:1 thrust-to-weight ratio) and top speed result in a model that performs much like a .46 glow engine-equipped version. And with fl ight durations of 8–15 minutes per charge, our electric powered Ultra Stick 40 delivers duration similar to that on a single tank of fuel. Best of all, installation of the Power 46 motor is easy with the battery packs and ESC being placed behind the fi rewall where the fuel tank would normally be mounted.
As an alternative to using the 4S2P 4200mAh Li-Po pack for powering the Power 46 motor and Ultra Stick 40, we also fl ew a 14-cell 3000mAh Ni-MH pack setup with very good results.
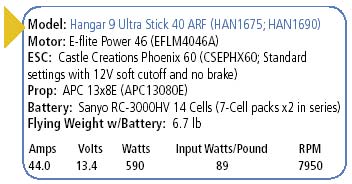
This power system setup delivers good performance with a good balance of thrust and top speed. Average duration is approximately 5–7 minutes per charge, depending on throttle management. With higher capacity cells in the same class (For example, 3600–3800mAh), duration could stretch to as much as 10 minutes per charge.
Let’s also take a quick look at the performance of a few more popular examples of power systems chosen by following the Input Watts Per Pound Guidelines:
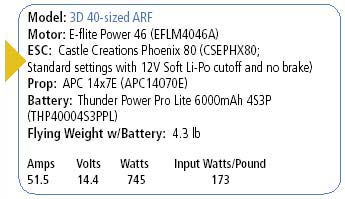
The performance of this model is very strong with unlimited vertical and plentiful power for hovering and 3D aerobatics. Average duration is approximately 15–20 minutes depending on throttle management. This power system setup is well suited for .25- to .40-sized 3D models up to 5-pounds all up weight.
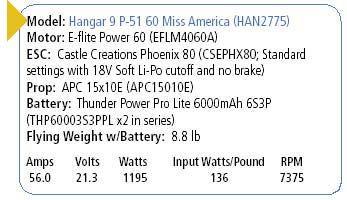
This power system setup delivers an excellent balance of thrust and top speed for the P-51. Average duration is approximately 8–15 minutes depending on throttle management. It’s well suited for a variety of .60-sized sport and warbird models (like the Hangar 9 Ultra Stick 60, P-47, Corsair and more).
The performance of this model is very strong with unlimited vertical and plentiful power for hovering and 3D aerobatics. Average duration is approximately 8-15 minutes depending on throttle management. This power system setup is well suited for 46-sized 3D models up to 7-pounds all up weight.
As you can see in these examples, by following the Input Watts Per Pound guidelines and calculating the power required to achieve our desired level of performance, we were able to determine the power needs of each model before selecting a power system. Then, with these power requirements in mind, and also by determining the power capabilities of a motor that could potentially be used to deliver the desired level of performance, we were also able to select a power system that would provide exactly the performance we were looking for. And by using the prop, ESC and battery sizes recommended in the manuals for use with the motors we chose for power, we were able to ensure solid and consistent performance of our power systems, flight after flight. But perhaps best of all, we got to enjoy all the benefits of a clean, quiet and smooth electric power system option with all the performance we would normally expect from a glow engine counterpart! |